Spray foam roofing can be an excellent investment for property owners seeking superior insulation, waterproofing, and energy efficiency. This roofing system creates a seamless, continuous barrier that eliminates thermal bridging while providing exceptional moisture protection. The decision depends on your building’s structural requirements, climate conditions, and long-term performance expectations.
Supreme Spray Foam LV has observed that most commercial and residential properties benefit significantly from spray foam roofing applications, particularly in Nevada’s challenging desert climate. Understanding the specific advantages, limitations, and installation requirements helps property owners make informed decisions about this advanced roofing technology.
Understanding Spray Foam Roofing Systems
Spray foam roofing utilizes polyurethane foam applied directly to existing roof surfaces, creating a monolithic membrane that expands and hardens upon contact. This process eliminates seams, joints, and penetrations that typically cause traditional roofing failures. The foam provides both insulation and waterproofing in a single application, making it particularly effective for flat and low-slope commercial buildings.
The system consists of two primary components: closed-cell spray foam base and protective coating layers. Closed-cell foam offers superior structural strength and moisture resistance compared to open-cell alternatives. The protective coating shields the foam from UV degradation and weather exposure, extending system lifespan significantly.
Bonus Tip: Schedule spray foam applications during moderate temperature conditions (between 40-85°F) for optimal foam expansion and adhesion. Extreme temperatures can compromise application quality and long-term performance.
Performance Characteristics and Benefits
Feature | Spray Foam Roofing | Traditional Built-Up | Single-Ply Membrane |
---|---|---|---|
R-Value per inch | 6.0-7.0 | 2.5-3.0 | 0.5-1.0 |
Seamless application | Yes | No | No |
Self-adhering | Yes | Requires adhesives | Requires fasteners |
Renewable surface | Yes | No | Limited |
Installation complexity | Moderate | High | Low |
Weather dependency | High | Moderate | Low |
Spray foam roofing insulation delivers exceptional thermal performance with R-values reaching 7.0 per inch of thickness. This superior insulation capability reduces energy consumption by 20-50% compared to conventional roofing systems, according to the Department of Energy’s commercial building energy efficiency studies. The seamless application eliminates common failure points found in traditional roofing methods.
The system’s self-adhering properties create strong bonds with various substrates, including concrete, metal, and existing roofing materials. This versatility allows for installation over most existing roof surfaces without complete tear-off, reducing project costs and environmental waste.
Technical Specifications and Requirements
Specification | Closed-Cell Requirements | Application Standards |
---|---|---|
Minimum thickness | 1.5 inches | ASTM C1029 |
Density | 2.0-2.5 lb/ft³ | ASTM D1622 |
Compressive strength | 25-30 psi | ASTM D1621 |
Thermal resistance | R-6 to R-7 per inch | ASTM C518 |
Fire rating | Class A available | ASTM E84 |
Wind uplift resistance | Up to 90 psf | ASTM E1592 |
Proper installation requires specific environmental conditions and professional expertise. Ambient temperature, humidity levels, and substrate moisture content directly impact foam quality and adhesion. Professional contractors monitor these variables throughout the application process to ensure optimal results.
Surface preparation proves critical for successful installations. Existing roofs must be structurally sound, clean, and dry before foam application. Any damaged areas require repair, and loose materials need removal to achieve proper adhesion.
Climate Considerations for Nevada Properties
Nevada’s desert climate presents unique challenges and advantages for spray foam roofing systems. Extreme temperature fluctuations, intense UV exposure, and low humidity levels affect system performance and longevity. The reflective coating systems commonly used with spray foam provide excellent heat reflection, reducing cooling loads during summer months.
The minimal precipitation in most Nevada regions reduces moisture-related concerns, while the intense solar radiation requires high-quality UV protective coatings. Properties in higher elevation areas may experience freeze-thaw cycles that benefit from spray foam’s seamless construction and thermal stability.
Bonus Tip: Select coating systems with high solar reflectance index (SRI) values exceeding 100 for optimal energy performance in Nevada’s intense sunlight conditions.
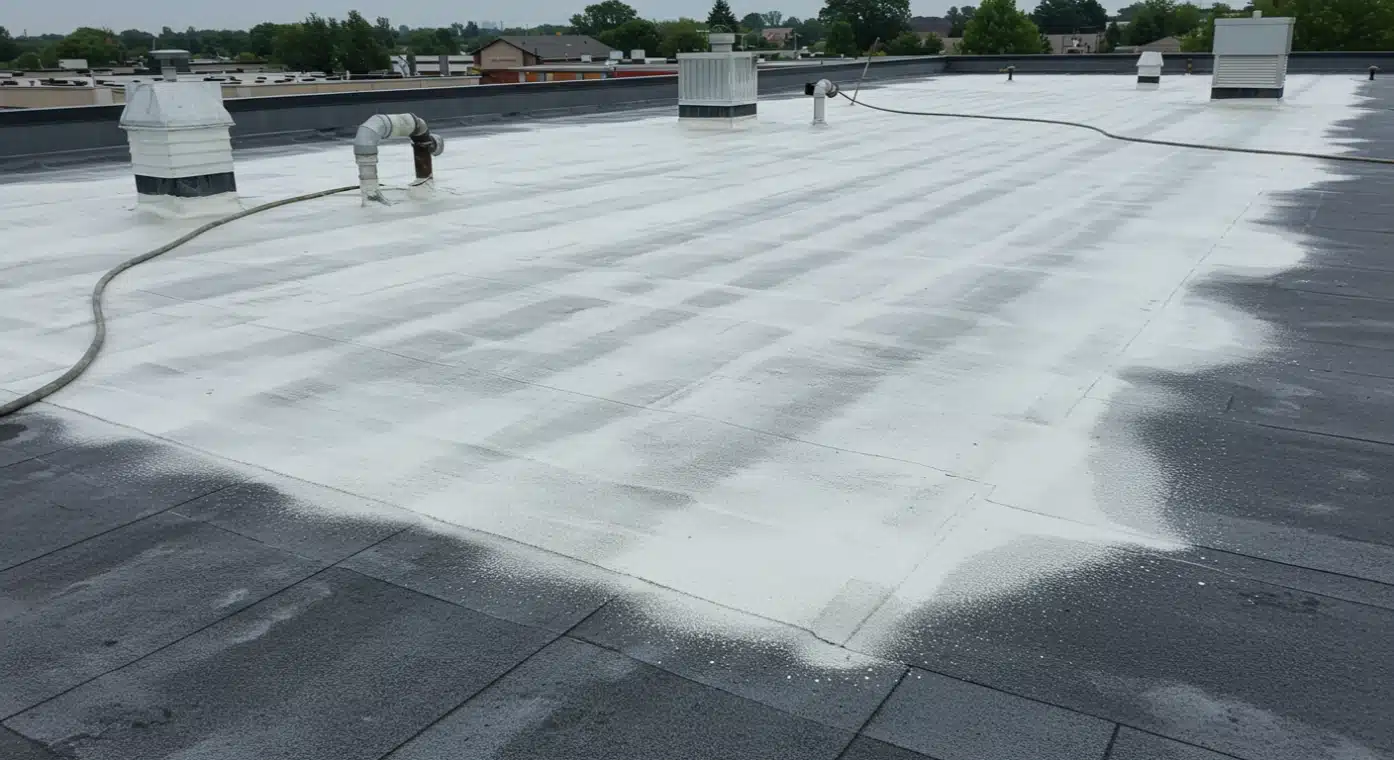
Things to Consider Before Making a Decision
Several factors influence spray foam roofing suitability for specific properties. Building age and structural condition determine whether existing roof systems can support additional foam weight and stress. Older buildings may require structural evaluations before installation proceeds.
Access requirements and building height affect installation complexity and costs. Multi-story buildings or properties with limited roof access may require specialized equipment and additional safety measures. Weather windows become critical in desert climates where afternoon winds and temperature extremes can halt application processes.
Budget considerations extend beyond initial installation costs. While spray foam insulation systems typically cost more upfront than conventional alternatives, the energy savings and extended lifespan often justify the investment. Maintenance requirements include periodic coating renewals every 10-15 years to maintain optimal performance.
Local building codes and permit requirements vary by jurisdiction. Some areas have specific requirements for foam thickness, fire ratings, or installation procedures. Consulting with local building departments ensures compliance with all applicable regulations.
Professional Installation Services Supreme Spray Foam LV Provides
Supreme Spray Foam LV specializes in comprehensive roofing insulation solutions designed for Nevada’s unique climate challenges:
- Commercial Spray Foam Insulation: Complete roofing systems for warehouses, office buildings, and industrial facilities with customized thickness and coating specifications
- Roofing Insulation: Specialized applications for flat and low-slope roofs using closed-cell foam technology with high-performance protective coatings
- Closed Cell Spray Foam Insulation: Premium density foam applications providing maximum thermal resistance and structural enhancement for demanding commercial applications
Common Questions About Spray Foam Roofing
How long does spray foam roofing installation take?
Most residential applications complete within 1-2 days, while commercial projects typically require 3-7 days depending on roof size and complexity. Weather conditions can extend timelines during unfavorable periods.
Can spray foam be applied over existing roofing materials?
Yes, spray foam adheres to most existing roof surfaces including built-up roofing, single-ply membranes, and metal roofing systems. However, substrate condition and compatibility must be evaluated before application.
What maintenance does spray foam roofing require?
Annual inspections and periodic coating renewals every 10-15 years maintain optimal performance. Immediate repair of any damaged areas prevents moisture infiltration and system degradation.
How does spray foam roofing perform in extreme weather?
Properly installed systems withstand high winds, hail, and temperature extremes. The seamless construction eliminates common failure points found in traditional roofing systems during severe weather events.
Bonus Tip: Document all maintenance activities and coating renewals to maintain warranty coverage and track system performance over time.
Energy Efficiency and Long-Term Performance
The National Roofing Contractors Association reports that spray foam roofing systems can last 20-30 years with proper maintenance, significantly longer than many traditional alternatives. The renewable coating surface allows property owners to refresh the system’s protective layer without complete replacement, extending useful life indefinitely.
Energy performance studies conducted by Oak Ridge National Laboratory demonstrate that spray foam roofing reduces cooling loads by 30-50% in hot climates. This translates to substantial utility cost savings over the system’s lifespan, often recovering initial investment within 5-8 years through reduced energy consumption.
The thermal bridging elimination provided by continuous foam application prevents heat transfer through structural components. This comprehensive thermal barrier approach proves particularly effective in commercial buildings with steel structural systems that conduct heat efficiently.
Making Your Roofing Decision
Evaluate your building’s specific requirements, climate exposure, and long-term occupancy plans before selecting any roofing system. Spray foam roofing offers superior performance for properties requiring maximum energy efficiency, waterproofing reliability, and extended service life. The investment typically proves worthwhile for buildings with high energy costs, frequent maintenance issues, or challenging weather exposure.
Consider consulting with an experienced spray foam roofing insulation contractor who understands local climate conditions and building requirements. Professional assessment ensures proper system design and installation methods suited to your specific application needs.
Get Expert Roofing Solutions Today
Transform your property’s energy efficiency and weather protection with professional spray foam roofing installation. Supreme Spray Foam LV provides comprehensive evaluations, professional installation, and ongoing maintenance support for commercial and residential properties throughout Nevada.
Contact our experienced team at (702) 904-9895 or email [email protected] to schedule your property assessment. Our specialists evaluate your specific requirements and provide detailed recommendations based on building characteristics, climate exposure, and performance objectives.
Addressing Long-Term Performance Questions
Will spray foam roofing increase property value?
Energy-efficient roofing systems typically increase property values by 3-5% according to commercial real estate studies. The documented energy savings and extended system life appeal to potential buyers and tenants.
How does spray foam roofing compare to solar installations?
The two technologies complement each other effectively. The excellent insulation reduces building energy loads, making solar systems more cost-effective by reducing required capacity.
What happens if spray foam roofing needs repairs?
Small damages can be easily repaired by applying additional foam and coating to affected areas. The seamless nature of the system allows for invisible repairs that maintain structural integrity.
Are there environmental benefits to spray foam roofing?
The system’s energy efficiency reduces carbon emissions over time, while the ability to install over existing roofing materials minimizes landfill waste from tear-off projects.
Can spray foam roofing support equipment installations?
Yes, the structural strength of closed-cell foam supports HVAC equipment, solar panels, and other rooftop installations when properly designed and installed.